The steam system on a tissue machine is critical not only to quality tissue production but also energy efficiency. Kadant, with its state-of-the-art W.R. Monroe Research & Development Center in Three Rivers, Michigan, USA, has invested decades into the study of even heat transfer in steam heated cylinders. It has also studied the reliable removal of condensate under an innumerable range of conditions.
The R&D center opened in May 1988 as the Johnson Research Center. At the company’s 60th anniversary in September 1993 it was renamed “W.R. Monroe Research & Development Center” in memory of William (Bill) Rollo Monroe, who served as President of the Johnson Corporation from 1957-1983 and then Chairman and CEO for his remaining tenure.
Innovative solutions to optimize your process
Importance of steam system surveys/audits
Regular (annual) steam system surveys are an important tool in maintaining the performance of a steam system. Steam systems will continue to function with poor performing equipment, typically from a lack of maintenance, but they will become inefficient. The performance often drifts gradually over time. This can lull operators into normalizing the newer, inefficient conditions, especially when their immediate attention is on other equipment. A loss of efficiency carries a real financial cost and can eventually lead to critical component failure and downtime. A typical steam system audit benchmarks the system’s performance against industry standards and identifies equipment that has failed or is failing. Prioritized areas of improvement are identified to help the client develop a process improvement plan. This is useful as the tissue industry becomes more resource conscious and minimizes its environmental impact.
Steam system survey case study
Kadant recently carried out a steam survey at a customer site. The customer’s aims were to identify energy savings at the plant as well as reduce the sites environmental impact. KADANT engineers studied the process for efficiency, potential bottlenecks and areas of improvement. Various sets of data were collected for performance analysis, including average monthly gas and water usage. The audit revealed the steam system had the potential of reducing its energy usage by 5% and CO2 output (carbon footprint) by 6%. It could improve condensate recovery by almost 24%. The energy and environmental inefficiencies identified were inherent to the legacy steam system design and not malfunctioning equipment, although some equipment was highlighted as needing attention. To realize the energy and environmental benefits Kadant proposed a steam system upgrade.

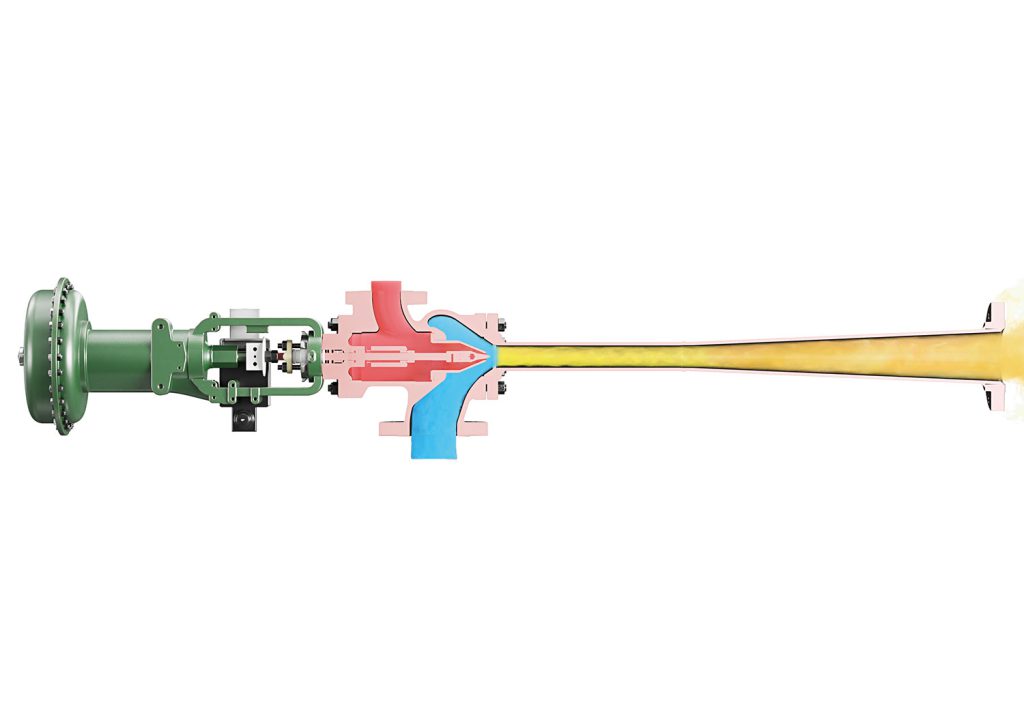
Kadant thermocompressor. Inset cutaway detail showing, “Red” motive steam flow, “Blue” flash (recovered) steam flow and “Yellow” discharge steam flow back into the Yankee dryer steam inlet.
Steam and condensate system upgrades
Kadant has an in-house design and project management team along with decades of specialized experience in steam system design. Kadant can offer turn-key and semi-turnkey solutions, depending on the end user’s internal projects, handling capacity and experience. A typical project starts by auditing the steam system to identify areas of improvement. These improvements are quantified so the client can calculate its return on investment (ROI). From this Kadant carries out detailed system design, which includes specialized Kadant hardware such as thermocompressors, which are a critical component of a tissue machine steam system. The detailed design is then passed to our in-house 3D piping design team, who will visit the site and take detailed measurements.
The piping design is a collaboration with the client, as each client’s needs differ. Once finalised piping designs are complete, the client can involve their own local piping contractor, or partner with Kadant to carry out the installation.
While the piping design phase is progressing, Kadant project engineers will specify and procure system equipment such as control valves, pumps and transmitters, ensuring they are delivered to the site on time for the shutdown. The final tasks include onsite supervision of the installation along with operator training and commissioning of the modernized steam system. Once up and running, the customer can expect to realize the benefits outlined in the steam system study.
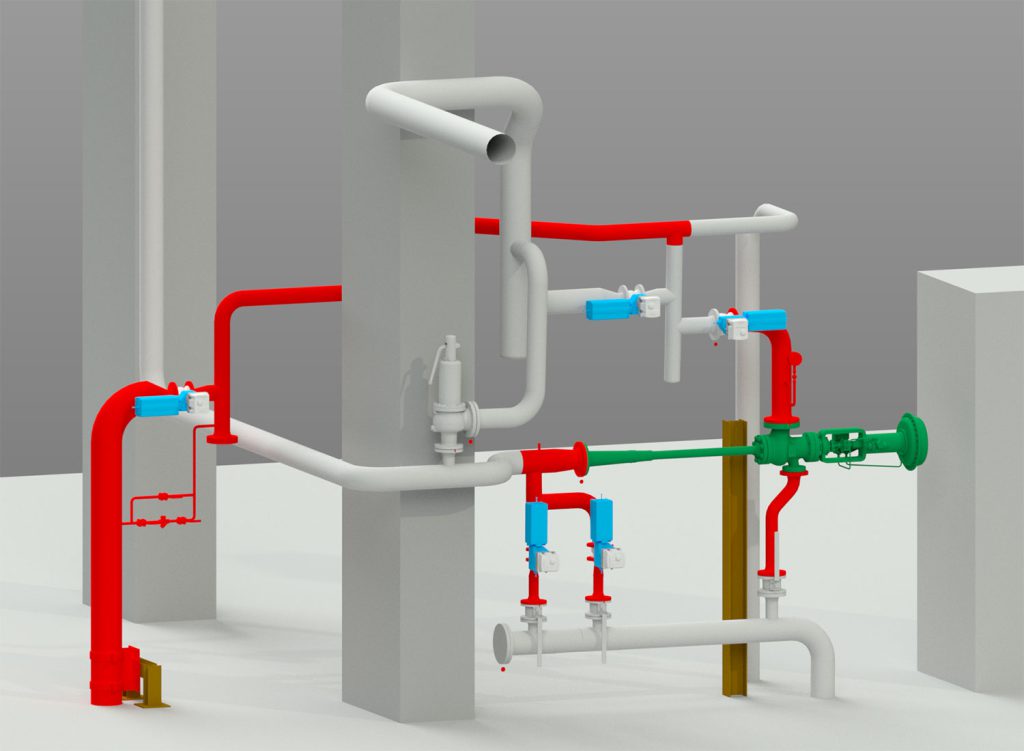